Operational Efficiency and Industrial Projects with Digital Twins
The Fourth Industrial Revolution is ushering in a new technological era in which industrial companies are becoming more efficient, innovative, and competitive. Two of the most transformative technologies in this context are Digital Twins and Big Data. These tools are not only optimizing processes but also changing the way industries manage production, maintenance, and decision-making.
What are Digital Twins?
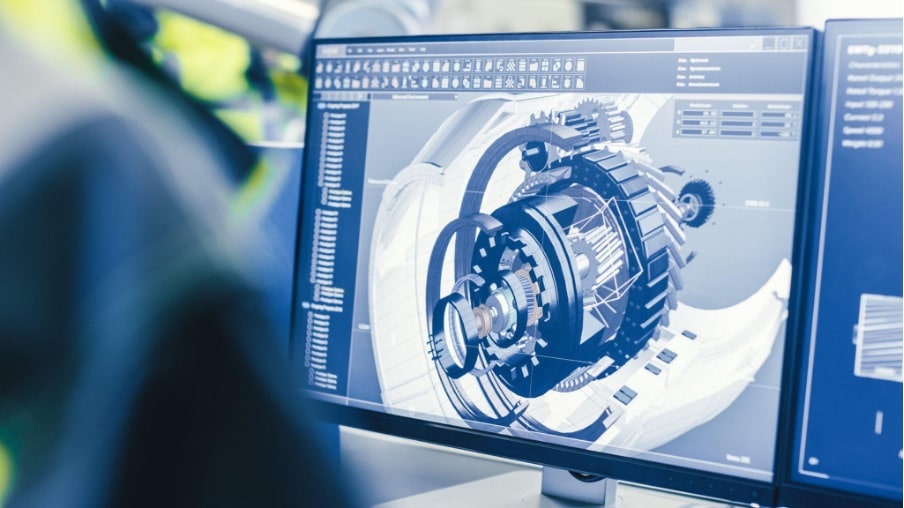
A Digital Twin is a digital replica of a physical system, allowing real-time simulation, analysis, and optimization of its behavior. The live data collected by Digital Twins provides valuable insights into the performance of equipment and processes.
– Real-time monitoring: Digital Twins continuously monitor operations, enabling early detection of issues before they become critical failures.
– Operational optimization: With the ability to simulate scenarios before implementation, companies can adjust processes to maximize efficiency and reduce costs
Big Data: The Power of Massive Data
Big Data refers to the collection and analysis of large volumes of data that cannot be handled by traditional methods. This massive processing capability is essential for extracting valuable insights from the data generated by industries.
– Predictive analytics: Big Data helps companies forecast future trends, enabling more accurate and proactive decision-making.
– Predictive maintenance: Analyzing historical and real-time data helps anticipate equipment failures, reducing downtime and unexpected costs.
The Synergy Between Digital Twins and Big Data
The combination of Digital Twins and Big Data is driving the Fourth Industrial Revolution, creating a synergy that enhances operational efficiency and fosters innovation across various industrial sectors.
1. Generation of valuable data: Digital Twins provide large volumes of data on the physical performance of equipment, which fuels Big Data analysis.
2. Advanced simulation and analysis: With Big Data, companies can analyze and predict the behavior of their Digital Twins, optimizing the decision-making process.
3. Continuous improvement: The feedback loop between Digital Twins and Big Data allows for constant adjustments in operations to maximize productivity.
Applications in the Industrial Revolution
– Smart Manufacturing: Smart factories are using Digital Twins and Big Data to optimize their production lines, simulating potential improvements without disrupting actual production.
Body
– Energy Management: Energy companies are using these technologies to manage the electrical grid more efficiently, adjusting supply and demand in real-time to reduce energy waste.
Conclusion
The Fourth Industrial Revolution is being driven by the power of Digital Twins and Big Data, technologies that are transforming how companies operate and make decisions. The combination of these tools is enhancing operational efficiency, reducing costs, and enabling greater adaptability to market demands. Companies that adopt these technologies will be better positioned to lead in this new industrial era.
Are you ready to join the Fourth Industrial Revolution with Digital Twins and Big Data?
JOIN THE NEW REALITY!