Digital Twin Applications for Real-Time Operations.
The world of technology is never stagnant, and the rise of digital twins has taken the industrial sector by storm. With the power to replicate physical assets in real time, these virtual objects are enabling organizations to gain deeper insights into their operations than ever before. From enhancing productivity and quality control to reducing downtime and maintenance costs, digital twin applications have revolutionized a variety of industries such as manufacturing, healthcare, automotive, aerospace, and defense among others.
So buckle up for an exciting read as we explore how businesses around the globe are leveraging digital twin technology for efficient real-time operations!
Digital twins are replicas of physical objects or systems that can be used to simulate real-world conditions and predict how the object or system will behave over time.
Digital twins can be used for a variety of applications, but they are particularly well suited for operations that need to be conducted in real-time, such as manufacturing, healthcare, energy production and distribution, transportation, and so on. The ability to monitor an industrial process in real time and make adjustments accordingly can result in significant efficiencies and cost savings.
There are many potential benefits of using digital twins for real-time operations; however, there are also some challenges that need to be addressed. One challenge is developing accurate models; another is ensuring that the data is precise and accurate.
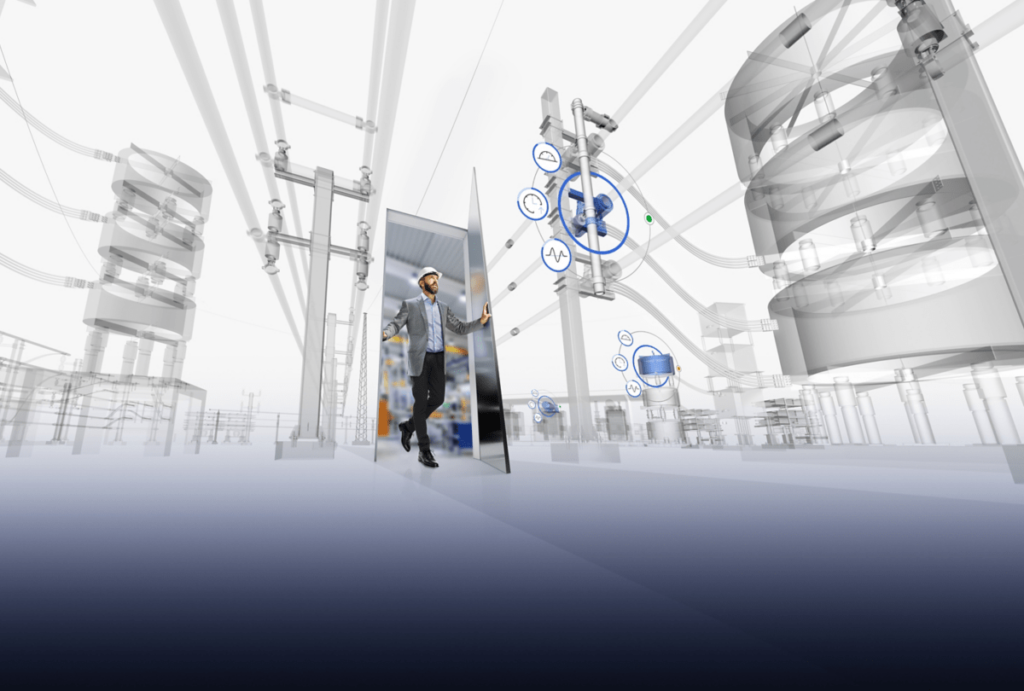
What are the Benefits of Digital Twin Technology for Real-Time Operations?
Digital twin technology can help organizations in a variety of industries to optimize their real-time operations. For example, manufacturers can use digital twins of their production lines to identify issues and correct them in near-real-time, before they result in downtime or quality problems. Retailers can use digital twins of their stores to monitor foot traffic and stock levels in real time and adjust staffing and inventory accordingly. And transportation companies can use digital twins of their routes and vehicles to plan and execute efficient, safe, and environmentally-friendly operations.
Applications and Use Cases of Digital Twin Technologies in Industry
Digital twins are becoming increasingly popular in a variety of industries as a way to manage real-time operations. Here we explore some main applications and use cases for digital twin technology.
In the industrial sector, digital twins are used to optimize production processes and improve quality control. For example, GE’s Predix platform is being used by Caterpillar to monitor the performance of its machines in real-time. This allows them to adjust the manufacturing process to improve efficiency and avoid downtime.
Digital twins are also being used in the oil and gas industry to help manage complex assets such as offshore platforms. ExxonMobil is using digital twins of its facilities to test different operational scenarios and make sure that its equipment can withstand harsh conditions.
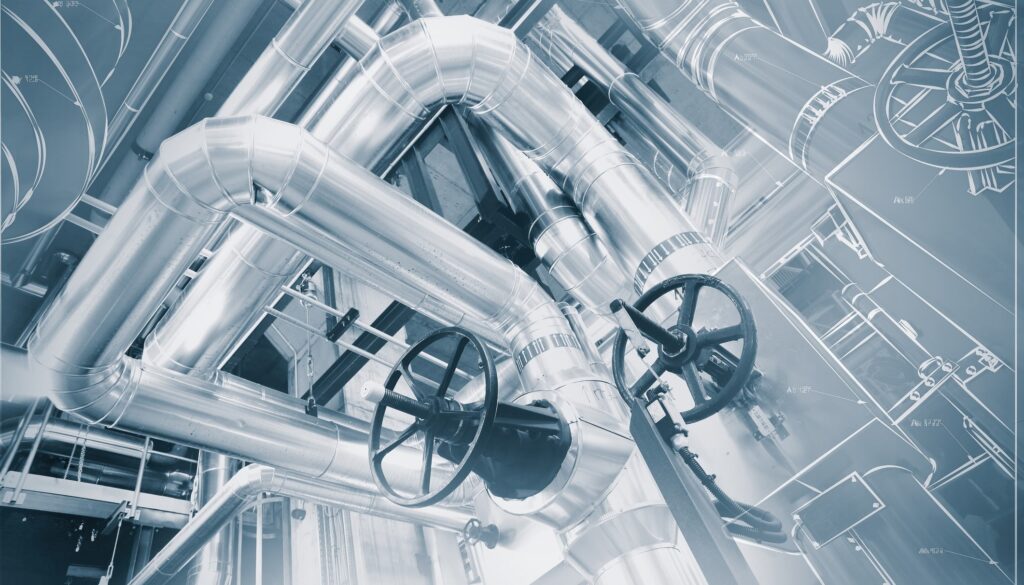
Another growing area for digital twin applications is in the construction sector. Here, they are being used to plan and manage construction projects, as well as track progress on-site in real-time. This allows for better coordination between different teams and contractors and helps avoid potential delays or issues with quality control.
Digital twins can provide the precise data needed for real-time operations, they are a great way to lower costs, improve products and services, and get better customer experiences. The opportunities digital twins open up have no boundaries. Whether you just want to monitor individual machines or an entire production line with live analytics of data collected from its components in real-time – all is possible through this emerging technology.
Join the new 4.0 digital age!